About Our Plant
Striving for a Plant of Worth Showing,
with Awareness of the Essence of GMP.
Manufacture of Ampoules
Manufacturing Environment
Ampoule forming is conducted in a completely sealed facility, learning from our past experience with environmental problems (i.e. contaminants, pollutants and variation of forming conditions) before building the Shiga Plant. The outside air is filtered before entering the workroom and the ventilation is automatically adjusted to ensure air cleanliness.
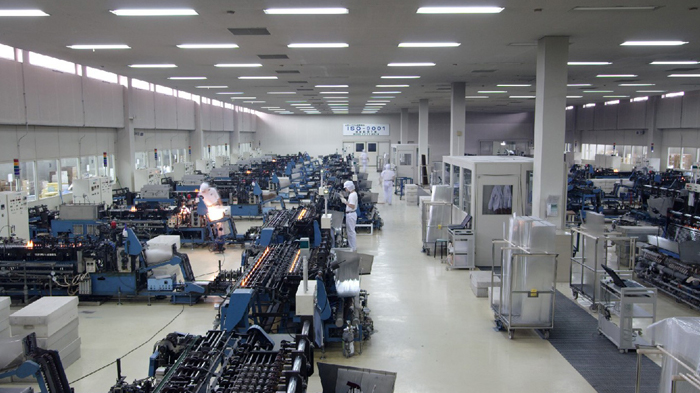
Completely sealed ampoule forming room
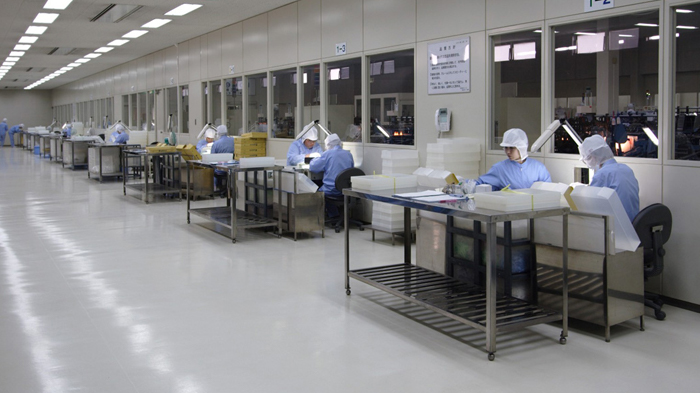
Ampoule visual inspection room
(100% manual inspection)
Production System
Ampoules are manufactured from glass tubing as raw material. Manufacturing ampoules used to be highly dependent on experienced workers’ skill and was therefore difficult to reproduce special quality attributes. Nowadays, however, we have succeeded in improving ampoule-forming machine by eliminating such craftsmanship as much as possible. For instance, we have introduced a method of controlling data on ampoule key dimensional measurements and burner flame adjustment, thereby realizing the today’s production system that can be handled by every operator (patented), and thus enabling the reproduction of special quality attributes which was very difficult in the past.
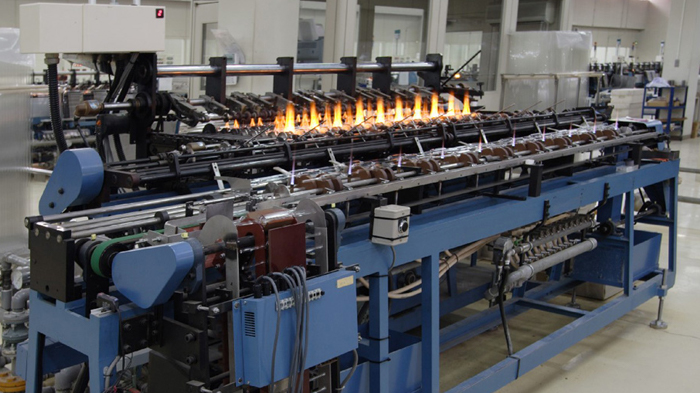
Extension machine
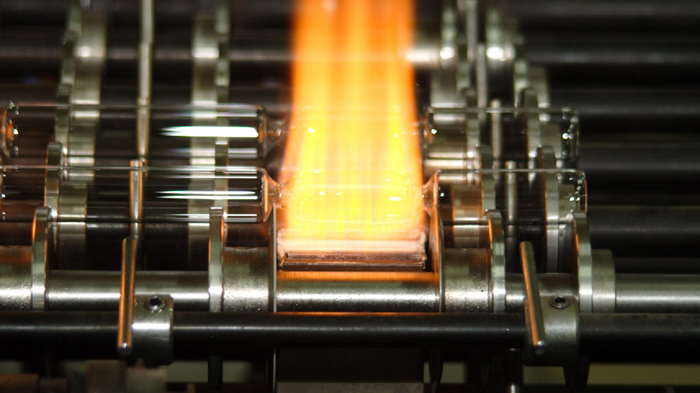
Extension process
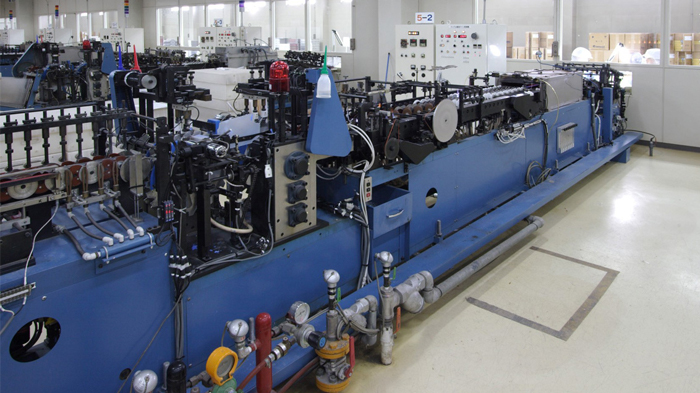
Bottom cutting machine
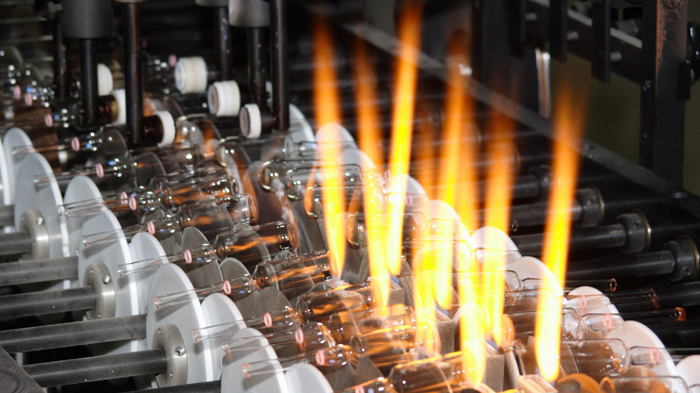
Bottom cutting process
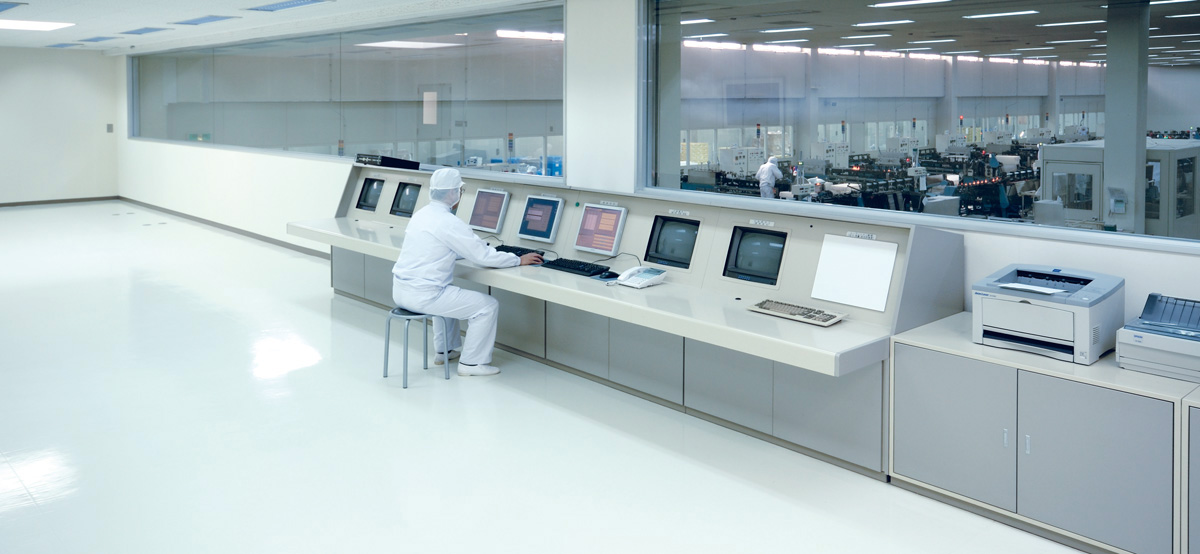
Control room for real time monitoring of ampoule key dimensions etc.
Various processing technologies
Various coating technologies are available tailored to customer’s demands, such as reducing alkali release from glass and preventing adsorption of drug solution to glass in micro-filling (low pH processing, sulfur treatment, silicone coating).